Machining with Torlon
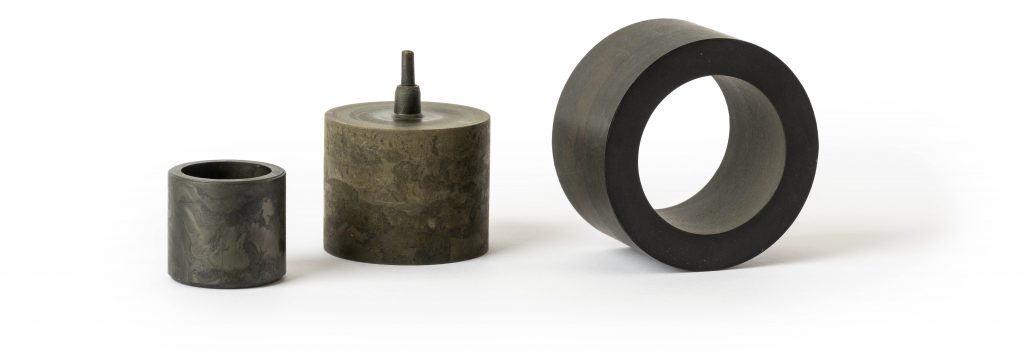
Torlon plastic is high strength and can withstand extremely hot and cold temperatures, as well as most chemicals, organic compounds, and acids. Plus, it can be machined using a variety of methods into highly precise shapes and specifications. These properties make it the best choice for replacing metal in a wide range of industries, including electronics, semiconductor, automotive, aerospace, and more.
Torlon machining tips
Torlon machining can take several different forms, including CNC milling, turning, drilling, sawing, or threading. Because Torlon is stronger and stiffer than most other plastics, it is recommended using carbide tooling on short runs and polycrystalline tooling on longer runs. Both of these materials can withstand the higher levels of abrasion produced by Torlon than softer plastics like nylon or acetal. Torlon also has lower elongation than many other plastics, so you should avoid excessive tool rubbing during machining to avoid cracking or void space.
Torlon CNC milling – We recommend part fixturing, high spindle speeds, and fast travel when completing Torlon milling to minimize frictional heat buildup. Plus, climb milling is better than conventional milling with Torlon machining for better chip removal, lower tool wear, and better surface finish.
Torlon turning – To avoid distortion, it’s best to use 360 degree chuck pressure. Internal plugs should be used to prevent thin walled Torlon parts from compressing and distorting.
Torlon drilling – Low helix drill bits and flood coolant are best for drilling holes in Torlon plastic. Coolant fed drills are ideal for removing swarf and preventing excessive heat buildup. Deep hole drilling without enough coolant can lead to cracking and other forms of breakage.
Torlon threading – It’s best to use single point inserts with flood coolant when threading Torlon plastic. Tapping for the inserts should be done with a cutting fluid.
Torlon sawing – Band sawing is the best method for cutting Torlon shapes. Blades should be chosen based on the thickness of your material and the level of precision required. Generally, fewer teeth per inch will help reduce heat buildup. Table sawing and chip sawing can also be used for Torlon machining.