Injection Molding with Torlon
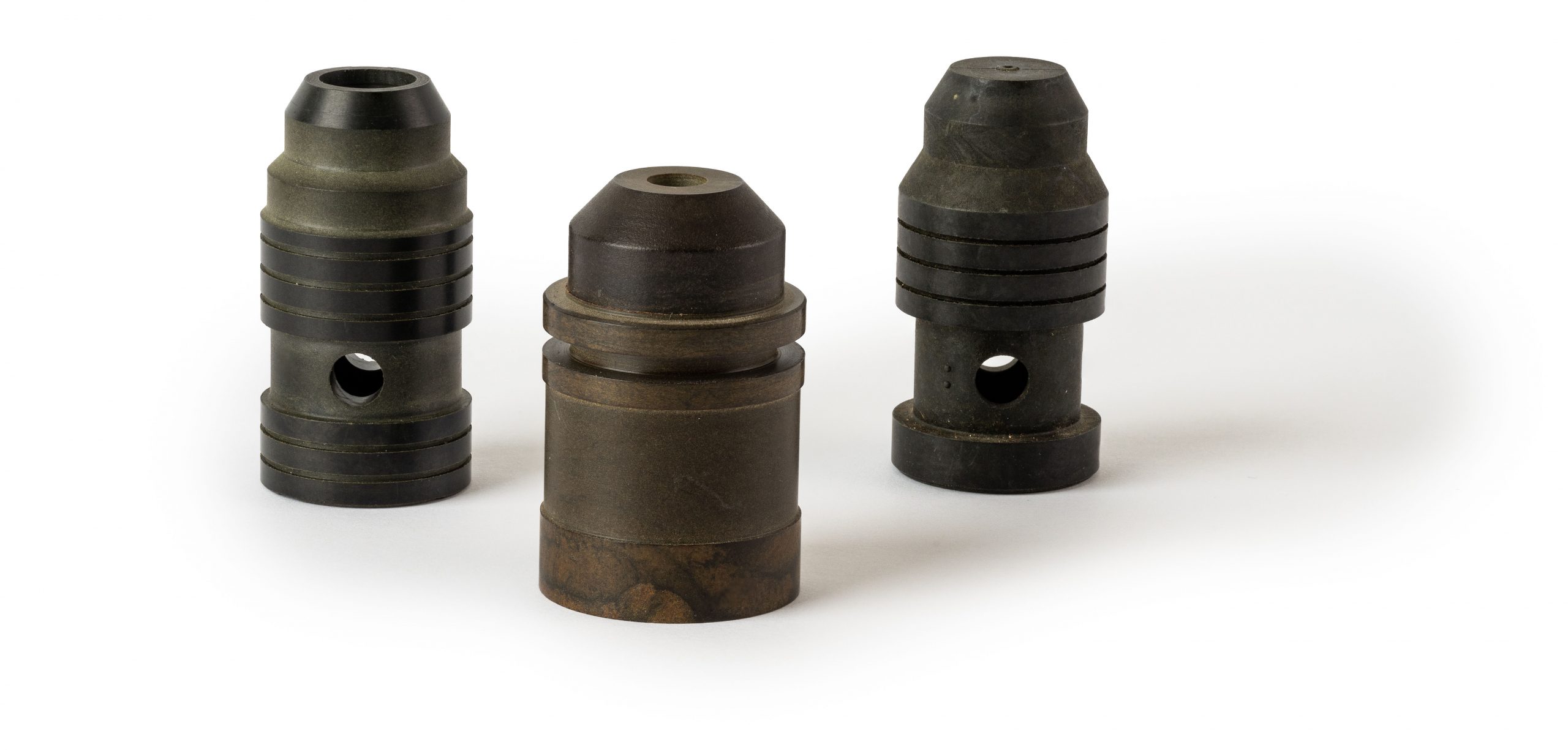
Due to its excellent performance under severe levels of temperatures, stress, and chemicals, Torlon plastic is an ideal choice for a wide range of structural and mechanical components. It operates better than any other thermoplastic, and it can be used to create more geometrically complex products than metal. Plus, it’s lightweight, quiet, and can be injection molded and machined to precise specifications.
Torlon injection molding
Injection molding is one of the most cost effective manufacturing processes for both large and small production runs of Torlon parts. It can be used to create highly complex parts, and it usually does not waste as much material as other processes, like CNC machining, which relies on cutting away material to reach the desired shape. Plus, Torlon has the highest tensile strength of all non-filled, injection moldable materials.
How injection molding works
Torlon injection molding looks very similar to other types of plastic injection molding. The Torlon begins as plastic pellets that are fed by an auger from a hopper into a barrel, which is then heated to melt the pellets. The molten Torlon then flows into a closed mold. Once cooled and solidified, the mold opens and your Torlon part is ejected from the machine.
Torlon specifics
Though Torlon is similar to other forms of plastic injection molding, there are some parts of the process that are specific to it:
- Equipment –Torlon injection molding requires a reciprocating screw machine with microprocessor controls capable of closed loop control. The barrel should be large enough so that 50% to 80% of the barrel is used for each shot to minimize residence time, and clamp tonnage should allow for at least 4 tons of clamp pressure per square inch of the projected part area. A low compression screw with no check device is best for Torlon.
- Drying requirements – Torlon resins require drying before injection molding. The drying machines should be capable of temperatures of at least 250 degrees Fahrenheit and maintain a dew point of -40 degrees Fahrenheit.
- Always purge the barrel – Torlon should not be left in the barrel of the injection molding machine during process interruptions or when the project is completed.
- Post cure – Torlon that has been injection molded must go through a post curing process to achieve the high performance capabilities this plastic is known for. Post curing involves placing the parts into a forced air oven and thermally treating them using a series of increasing temperatures for varying lengths of time.