Advantages of Using Torlon Plastic
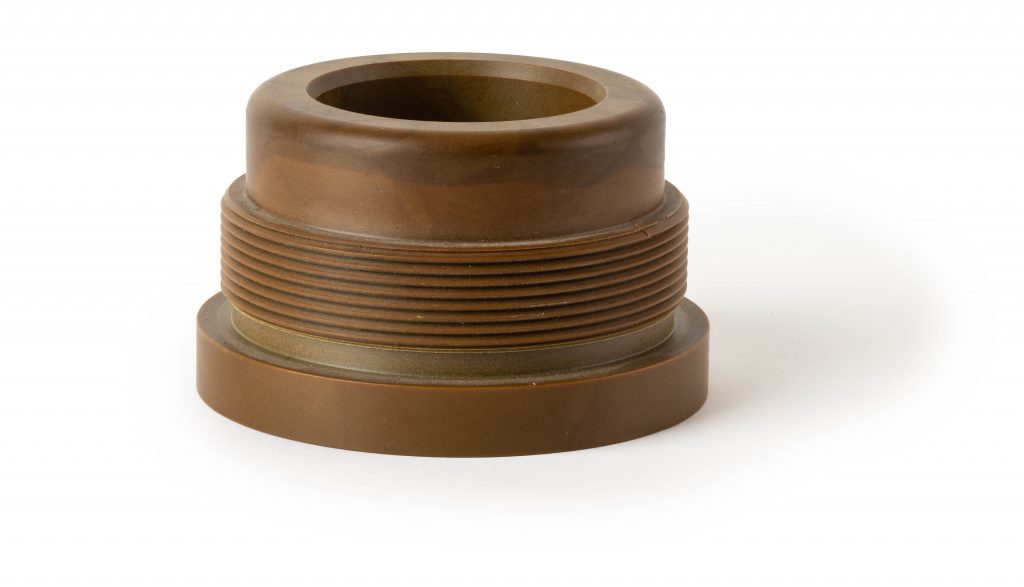
Torlon is one of the highest performance thermoplastics available. Due to its reliability in severe high and low temperatures and under stress, this material is a smart choice for manufacturing critical mechanical and structural components for aircraft, automotive transmissions, heavy duty equipment, and more.
Torlon plastic can handle the toughest conditions
Torlon plastic checks all the boxes when it comes to operating in extreme environments. It maintains strength, stiffness, and impact resistance at continuous very low temperatures and temperatures as high as 500°F, plus it’s virtually unaffected by many chemicals, including acids and organics. In addition, Torlon performs well in both dry and lubricated environments and features excellent resistance to radiation, wear, and creep, which means it won’t deform easily under stress.
Metal replacement
Manufacturers are turning more and more to plastic alternatives instead of metal to create parts and components. In addition to being strong under tough conditions, Torlon plastic is an ideal candidate for many more reasons:
- It reduces costs – Injection molding and machining with Torlon plastic uses less labor and energy compared to metal fabrication processes.
- It can be used to create more geometrically complex products – With Torlon plastic you can produce complicated products. Developing the same types of products with metal is more difficult and expensive, and options are often limited.
- It’s lightweight – Torlon is about half the weight of aluminum, 1/6 the weight of steel and even lighter compared to many other metals. For automobile and aircraft components, manufacturers need materials that can reduce the overall weight while maintaining toughness and heavy duty features.
- Quieter components – Parts made from Torlon are generally much quieter than their metal counterparts, which is important for automobile, aircraft, and equipment applications.
- Performs well in hot environments - Torlon has a very low CLTE rating, so it won’t expand or contract much with temperature changes, and it has low flammability properties and will generate very little smoke.
Versatile manufacturing options
The other benefit of using Torlon plastic is that you have multiple production methods available to you. Manufacturers can use plastic injection molding, machining, and grinding to create highly precise products that meet exact specifications. There are also a number of different grades that are ideally suited to specific applications. Below is a list of Torlon grades available, and common uses are shown for each grade.
Torlon 4203 - Electrical connectors, insulators, and rollers, balls, and seals
Torlon 4275 - Bearings, thrust washers, wear rings, bushings
Torlon 4301 - Compressor parts, bear cages, seals
Torlon 4435 - Sliding vanes, piston rings, thrust washers
Torlon 4601 - Bearings, industrial equipment components
Torlon 4630 - Thrust washers, seal rings, bobbins, clutch rollers
Torlon 4645 - Connectors, gears, impellers, seals
Torlon 5030 - Structural parts, electrical insulators, thermal isolating components
Torlon 7130 - Aerospace parts, impellers, pistons, shrouds, housings
Specialty Polymers
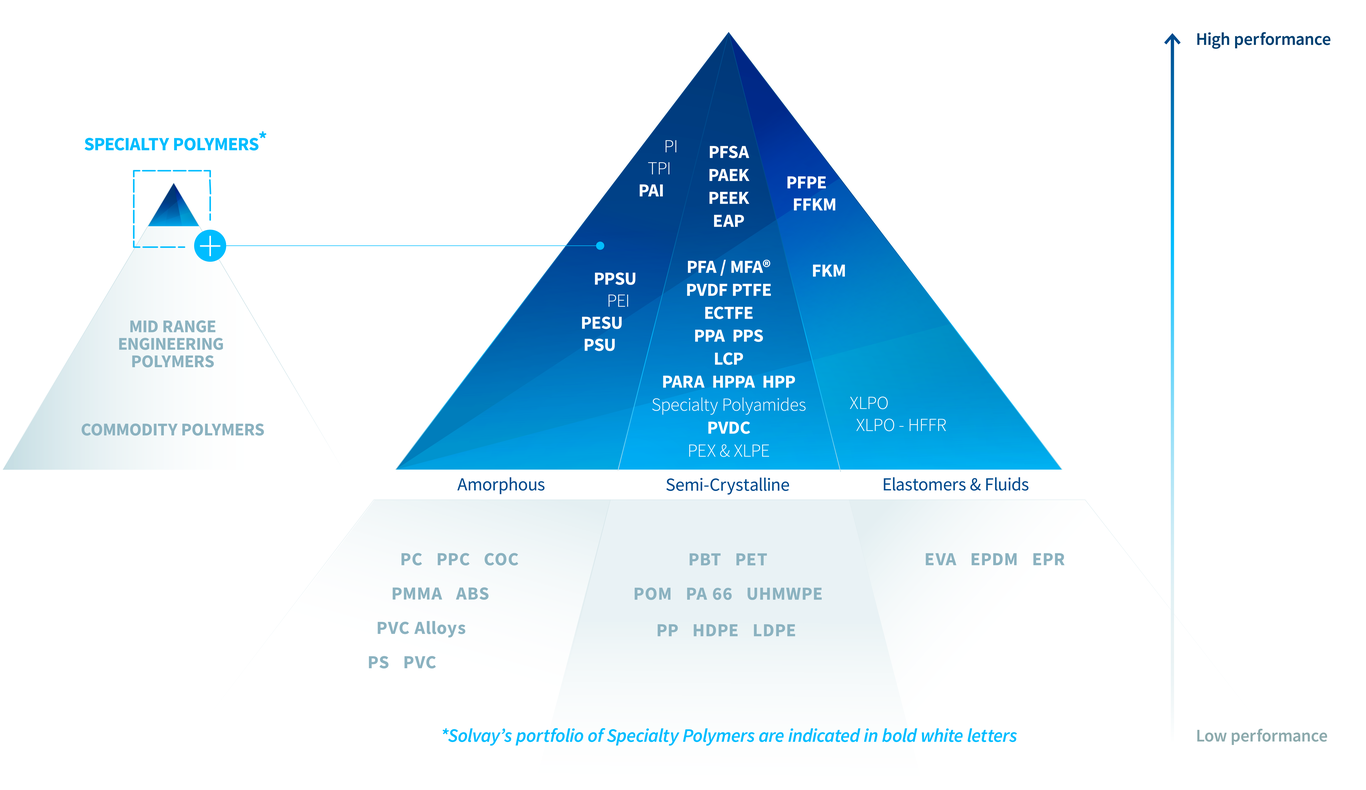